LDPE for Plastic Bag Manufacturing
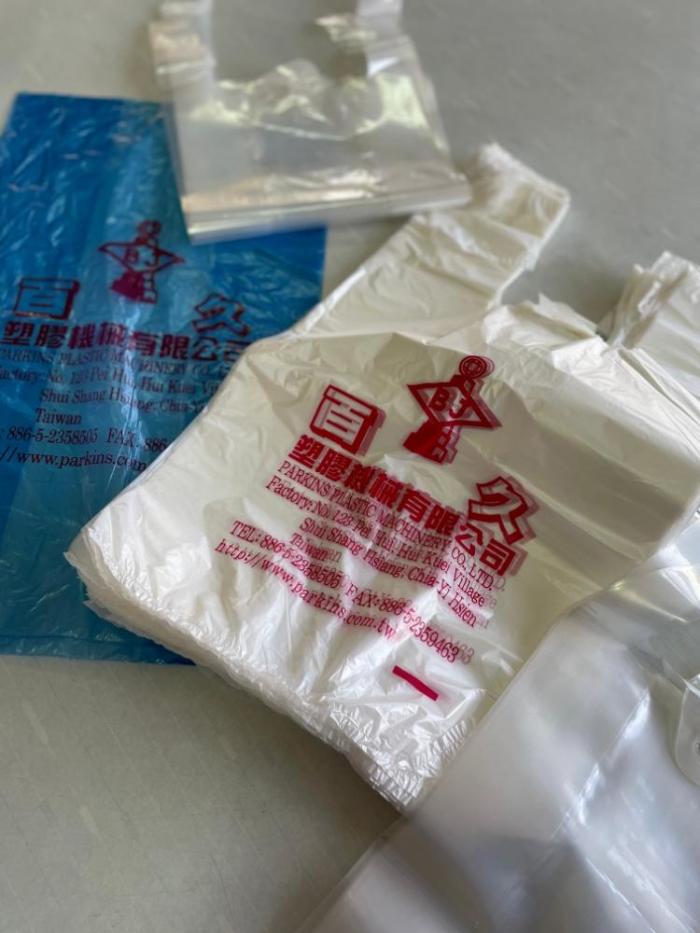
What is LDPE?
LDPE (Low-Density Polyethylene) is a widely used thermoplastic polymer known for its low density, softness, and excellent flexibility. As one of the most common types of polyethylene, LDPE is produced through a high-pressure polymerization process that results in a highly branched molecular structure. This structure gives LDPE its unique physical characteristics, such as high ductility, low tensile strength, and exceptional resistance to impact, chemicals, and moisture.
In the packaging industry, LDPE plays a crucial role due to its ability to form thin, transparent films that are lightweight yet durable. It is frequently used in the production of everyday items such as plastic bags, shrink films, bubble wraps, and various food-grade packaging materials. From retail and grocery bags to industrial liners and food storage solutions, LDPE continues to be a preferred material for manufacturers seeking cost-effective, versatile, and process-friendly plastic packaging.
As global demand grows for sustainable packaging solutions, many producers are also exploring blends of LDPE with recycled or biodegradable materials, without sacrificing compatibility with their existing LDPE plastic bag making machines.
Benefits of Using LDPE in Plastic Bag Making Machines
LDPE offers unique processing advantages that make it suitable for bag production:
Flexibility and Elasticity
LDPE has excellent softness and ductility, making it suitable for packaging that requires good sealability and foldability.
Transparency
LDPE offers a certain degree of transparency, enhancing product visibility—ideal for display packaging.
Water and Moisture Resistance
Its molecular structure provides strong resistance to water and moisture, effectively blocking vapor penetration.
Chemical Resistance
LDPE is resistant to most acids, alkalis, and solvents, making it suitable for a variety of industrial packaging applications.
Bag Making with LDPE: Machine Compatibility
Producing LDPE bags requires specialized equipment that can handle its low melting point and soft nature. LDPE plastic bag making machines are designed with optimized temperature control, film feeding precision, and sealing mechanisms to accommodate LDPE’s specific material characteristics.
Common bag types made with LDPE bag making machines include:
- Food packaging bags (e.g., frozen food bags, bread bags)
- Industrial packaging films and bags (e.g., dust-proof bags, inner cushioning bags)
- Grocery and shopping bags
- Garbage and cleaning bags
- Agricultural films and packaging films
Our LDPE plastic bag making machines support both single-layer and multi-layer LDPE film applications, with options for automatic cutting, sealing, punching, and stacking. Whether you're starting a new production line or upgrading an existing one, we offer tailored solutions for efficient LDPE bag manufacturing.
Environmental Impact and Recyclability of LDPE
LDPE is classified as plastic #4 and is recyclable. However, its soft texture can pose challenges in the recycling process, as it may easily entangle recycling machinery. With advancements in recycling technologies, our LDPE-compatible machines are designed to work with recycled LDPE film and even biodegradable LDPE blends, supporting a more circular production model.
Pros and Cons of LDPE for Plastic Bag Production
Advantages | Disadvantages |
Excellent flexibility and elongation |
Not biodegradable; requires proper recycling |
Low cost and easy to process |
Lower strength and heat resistance |
Good water, moisture, and chemical resistance |
Not suitable for high-temperature applications (melting point approx. 105–115°C) |
Moderate transparency and glossiness |
Easily scratched and not very wear-resistant |
Why Parkins LDPE Bag Making Machines?
When it comes to producing high-quality LDPE plastic bags, choosing the right machinery is just as important as the material itself. Parkins LDPE bag making machines are specifically engineered to handle the unique properties of LDPE film, offering precision temperature control, smooth film feeding, and efficient sealing performance.
LDPE remains a vital material in the plastic bag industry due to its flexibility, moisture resistance, and cost-efficiency. When paired with the right equipment, such as Parkins' advanced LDPE plastic bag making machines, manufacturers can produce high-quality packaging while meeting both operational and sustainability goals. As the industry continues to evolve, Parkins remains committed to providing smart, efficient, and future-ready bag making solutions for your LDPE production needs.
FAQs About LDPE Bag Making and Machines
Q: What features should I look for in an LDPE plastic bag making machine?
A: Key features include precise temperature control, high-speed operation, compatibility with soft and stretchy films, automatic sealing and cutting, and customization for bag shapes or printing needs. Machines should also support recycled LDPE materials if sustainability is a concern.
Q: Is there a difference between LDPE and HDPE bag making machines?
A: Yes. LDPE has a lower melting point and higher flexibility than HDPE. Machines designed for LDPE require more accurate sealing temperature control and smooth film feeding systems to prevent wrinkling or film distortion. Some machines are adjustable to run both materials, but dedicated machines yield better performance.
Q: Can Parkins LDPE bag making machines work with biodegradable LDPE blends?
A: Yes. Parkins machines are compatible with biodegradable or compostable LDPE-based films, offering manufacturers the ability to produce more eco-friendly packaging solutions without changing core machinery.
Q: What is the production speed of an LDPE bag making machine?
A: Production speed depends on the bag size, film thickness, and machine model. Parkins LDPE bag making machines typically offer high-speed performance with advanced automation, reaching up to hundreds of bags per minute under optimal settings.
Q: Is it possible to use recycled LDPE film with Parkins machines?
A: Absolutely. Our LDPE plastic bag making machines are designed to accommodate both virgin and recycled LDPE film. However, using recycled material may require slight adjustments to temperature and tension settings to maintain bag quality.
Q: What maintenance is required for an LDPE bag making machine?
A: Regular maintenance includes cleaning sealing components, checking tension rollers, replacing wear parts, and software calibration. Parkins provides detailed manuals and remote technical support to ensure your machines run smoothly with minimal downtime.
Q: Do you offer customized solutions for specific LDPE bag applications?
A: Yes. Parkins offers custom solutions to meet different production needs, whether you're making large-format garbage bags, perforated roll bags, or bags with side gussets. Customization is available for machine size, output, unwinder options, and automation level.