Future of Eco-Materials
How Sustainable Materials Influence Biodegradable Plastic Bag Making
The rise of sustainable materials is reshaping the way manufacturers approach biodegradable plastic bag making. While bio-based and compostable plastics have gained traction in the market, they still present several challenges, particularly in terms of cost, material performance, and the specific environmental conditions required for proper degradation.
For instance, many biodegradable plastics take longer to break down in natural settings and may require industrial composting facilities to achieve complete decomposition. Similarly, while plant-based and recycled plastics help reduce reliance on virgin plastic, they are not inherently pollution-free and still need to be managed responsibly to avoid long-term environmental impact.
Despite these limitations, sustainable materials are playing a pivotal role in the evolution of the industry. The increasing adoption of bio plastic bag making machines is helping manufacturers efficiently process newer, more eco-friendly materials. As technology advances and environmental policies continue to evolve, we can expect a broader transformation in plastic bag production, driven by improved bio-material research, enhanced recycling processes, and greater market acceptance of compostable solutions.
This shift not only supports more sustainable manufacturing practices but also opens the door to innovative packaging options that align with global sustainability goals.
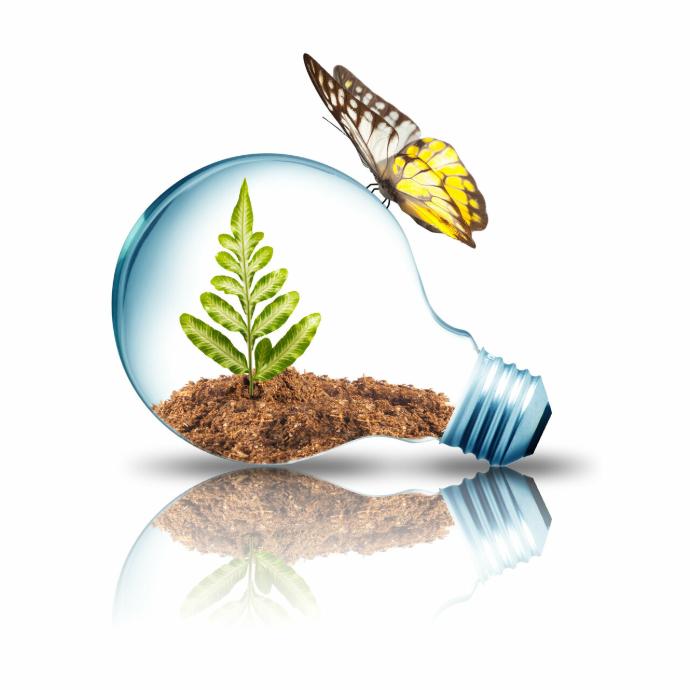
Common Challenges in the Bag-Making Industry
When it comes to production and manufacturing in the bag-making industry, several pain points frequently arise. Based on its extensive industry experience, Parkins provides the following solutions to help you upgrade your production line
1. Standard Machines Cannot Meet Specialized Needs
The industry demands a wide variety of products, particularly in the production of food packaging and eco-friendly plastic bags, where specific requirements exist for bag size, material, and sealing methods. However, standard machines on the market often lack the flexibility to adapt to these needs, posing challenges to the production process.
Parkins Machinery Solutions:
Customizable Services: We offer highly tailored solutions, adjusting machine structures and functions to meet industry requirements, such as compatibility with LDPE, HDPE, recycled materials, and more. We also design modules for various sealing techniques.
Technical Planning Consultancy: Our expert team analyzes your production line and needs, offering optimized equipment combinations to enhance production flexibility.
2. High Costs of High-Performance Equipment
High-performance equipment often comes with steep initial investment costs. While these machines excel in production capabilities, concerns about long-term operational and maintenance expenses can make total costs difficult to control.
Parkins Machinery Solutions:
Cost-Effectiveness Analysis: We provide a comprehensive assessment, from acquisition to operation, helping you evaluate long-term savings (e.g., energy-efficient designs that reduce power consumption).
Energy-Saving Technologies & Subsidies: Our equipment incorporates energy-saving designs to lower energy usage. We also assist in applying for government low-carbon or environmental subsidies to reduce upfront costs.
Reduced Maintenance Costs: Our equipment parts are CNC-precision processed, significantly
reducing the frequency of maintenance and part replacements, ensuring
maintenance costs remain transparent and manageable.
3.Complexity of Operating High-Tech Equipment
Concerns about the complexity of high-tech equipment operations often arise, as lengthy staff training can hinder initial production efficiency. Additionally, a lack of experience in maintenance can further complicate equipment adoption.
Parkins Machinery Solutions:
User-Friendly Interface: Our machines feature intuitive smart touchscreens with multilingual support, making operations straightforward and reducing the learning curve for employees.
Comprehensive Training and Support: After installation, we provide full operational and maintenance training, with dedicated professionals offering remote technical assistance to address any challenges.
Intelligent Automation: Built-in automatic detection systems warn of potential issues before breakdowns occur, offering peace of mind for your team.
4. Insufficient Production Quality and Stability
High-volume production demands consistent, high-quality output. Any minor production quality issues can lead to customer complaints and material waste. Concerns also arise about whether equipment can maintain long-term operational stability.
Parkins Machinery Solutions:
High-Precision Components: Our parts are CNC-precision processed and undergo multiple tests before delivery to ensure machine durability and operational stability.
Stable Production Design: We optimize the machine structure for prolonged operation, effectively preventing instability caused by heat or mechanical wear.
5. Lack of After-Sales Support and Upgrades
Is there a comprehensive after-sales service? Especially in terms of equipment upgrades and part replacements, sustained support is essential to avoid one-time transactional cooperation. At Parkins, we aim to be your long-term partner by providing complete after-sales services.
Parkins Machinery Solutions:
Rapid Response Mechanism: We maintain a well-stocked inventory of parts and repair services to resolve equipment issues promptly, minimizing downtime risks.
Upgrades and Continuous Improvement: Based on market demands and customer feedback, we offer software and hardware upgrades to ensure your equipment remains competitive.
Regular Follow-Ups and Inspections: We proactively arrange follow-up calls or visits to check equipment performance and provide improvement suggestions tailored to your needs.
Parkins Biodegradable Plastic Bag Making Machine Series
Parkins provides specialized bio plastic bag making machines designed to handle eco-friendly materials such as PLA, PBAT, and other compostable films. Our eco-friendly plastic bags making machine ensures efficient production without compromising material integrity, helping our customers transition to sustainable packaging solutions with confidence.
Driving Sustainability with Parkins: NuPlastiQ®
Parkins is committed to driving sustainable innovation in the plastic bag manufacturing industry. As global demand for environmentally responsible packaging grows, we provide advanced bioplastic bags manufacturing machines that empower manufacturers to adopt greener practices without sacrificing performance or efficiency.
Our machines are designed to work seamlessly with a wide range of sustainable materials, supporting efforts to reduce plastic waste and lower environmental impact. Among these materials, NuPlastiQ® stands out for its unique balance of strength, versatility, and eco-friendliness.
NuPlastiQ®: A Plant-Based Biopolymer for Sustainable Plastics
NuPlastiQ®, made with 100% plant-based biopolymers, is a unique thermoplastic resin that decomposes relatively quickly in natural environments, unlike traditional plastic bags which persist in soil or water for extended periods. These alternatives are intended to reduce the environmental impact of traditional plastic bags, such as their harm to marine life and the negative effects of plastic waste on the Earth's ecosystem.
Produced using proprietary processes, high-crystallinity starch powder is converted into low-crystallinity (mostly amorphous) plastic resin. NuPlastiQ is provided in pellet form. This thermoplastic material, when combined with mainstream high-performance polymers, offers many characteristics suitable for manufacturing a variety of products, including films and bags, injection-molded parts, blow-molded bottles, and thermoformed parts. NuPlastiQ's unique properties allow it to easily blend with other plastic resins, including fossil fuel-based and bio-based materials. It is directly compatible with polyolefins (PE, PP, PS) and compostable (PLA, PBAT, PHA) materials.
Why Choose Sustainable Materials?
Using sustainable materials helps alleviate the strain on Earth's resources, reduce environmental pollution, and foster a transition toward sustainable development.
Sustainable materials (or eco-friendly materials) are those that have a lower environmental impact during production, use, and disposal.
These materials typically exhibit the following characteristics:
Renewability
These materials come from renewable resources, such as plants, recycled materials, or regenerated materials, while maintaining the ability to replenish these resources during production.
Low Environmental Impact
The production and use of these materials generate fewer greenhouse gases, pollutants, and waste, reducing negative impacts on the natural environment. By using filtration equipment and recyclable materials, air pollution and waste generated during production can be minimized.
Reduced Carbon Emissions
Using sustainable materials can reduce the carbon footprint throughout the product life cycle, helping to lessen the environmental burden.
Improved Energy Efficiency
Sustainable production designs often incorporate insulation materials and ventilation systems, which reduce energy consumption during the production process and enhance efficiency.
Lifecycle Management
Sustainable materials consider the entire lifecycle of a product—from production and use to maintenance and disposal—aiming to minimize resource consumption and waste generation.
Resource Recycling
The use of biodegradable or recyclable packaging reduces waste and contributes to the promotion of resource recycling.
Supply Chain Social
Responsibility
Sustainable production adheres to social and ethical standards, ensuring worker rights and supporting socio-economic systems geared towards sustainable development. Ensuring suppliers meet environmental and social responsibility standards helps promote the sustainable development of the overall supply chain.
Obtain Relevant Subsidies
Using equipment and materials that meet environmental requirements may allow companies to qualify for low-carbon subsidies, reducing some production costs.
Respond to Market Demand
The application of sustainable materials can meet some consumer demands for environmental protection, enhancing the market acceptance of the products.
What Sustainable Materials Are Suitable for Bag-Making Industry?
With the growing global environmental protection awareness, the plastic bag industry is undergoing significant changes, gradually moving toward sustainable development. Bio-plastic bag making machines are at the forefront of this transformation, enabling the production of more environmentally responsible packaging solutions.
Plastic bags are widely used in daily life, but traditional plastic bags have low durability and degradability, making them difficult to break down in the natural environment, which poses challenges to ecosystems. To reduce the environmental impact of plastic waste, more and more companies and manufacturers are starting to adopt sustainable materials in their production processes. By utilizing an eco-friendly plastic bags making machine, businesses can create packaging that is both functional and eco-conscious.
Below are several common sustainable materials applied in plastic bags:
Sustainable Materials for a Greener Future in Bag-Making
By adopting these sustainable materials, the bag-making industry can align with global environmental goals and reduce its ecological footprint. With the help of biodegradable plastic bag making machines, manufacturers can efficiently produce eco-friendly bags that contribute to reducing plastic waste.
Parkins Machinery is your comprehensive solution provider for addressing production pain points and enhancing bag-making operations. Whether you're tackling production challenges or transitioning to sustainable manufacturing with biodegradable plastic bag manufacturing machines, Parkins Machinery is your most reliable partner in creating innovative and sustainable packaging solutions.
1. Biodegradable Plastics
Biodegradable plastics are materials that can break down into water, carbon dioxide, and organic matter in the natural environment. Under ideal conditions, they can fully decompose without producing permanent microplastic particles. Common biodegradable plastics include polylactic acid (PLA) and polyhydroxyalkanoates (PHA). PLA is mainly derived from plants like corn starch and is a popular biodegradable material, widely used in plastic bags and other packaging materials. These materials can decompose completely under composting conditions, making them a choice for many retailers.
Characteristics:
These plastics decompose naturally into water, carbon dioxide, and biomass, reducing waste accumulation.
Common types:
PLA (Polylactic Acid): Made from renewable resources like corn starch and sugarcane.
PHA (Polyhydroxyalkanoates): Biodegradable polyester synthesized by microorganisms.
PBAT (Polybutylene Adipate Terephthalate): Known for its flexibility and often blended with PLA.
2. Compostable Materials
Compostable materials are usually made from bio-based materials like PLA and meet specific composting standards, such as Europe’s EN 13432 or the US ASTM D6400. These materials can completely degrade into harmless substances under industrial composting conditions and are commonly found in shopping bags used in supermarkets and retail sectors. The advantage of compostable materials is that they degrade in specific composting environments, reducing the environmental impact of plastic waste and offering consumers a more eco-friendly option.
Characteristics:
Fully decomposes into harmless substances under industrial composting conditions.
Meets standards like EN 13432 (Europe) or ASTM D6400 (USA).
Typically based on PLA and plant fibers.
3. Recycled Plastics
Recycled plastics are made by reprocessing plastic waste, primarily including recycled PET (Polyethylene Terephthalate) and HDPE (High-Density Polyethylene). Using recycled plastics helps extend the lifespan of materials and reduces the demand for virgin plastics. While recycled plastics are not biodegradable, their recycling properties play a crucial role in reducing environmental impact.
Characteristics:
Made from recycled plastics such as PET (Polyethylene Terephthalate) or HDPE (High-Density Polyethylene).
While not entirely eco-friendly, they extend the life of plastics and reduce the demand for virgin plastics.
4. Bio-Based Plastics
Bio-Based Plastics (Plant-based plastics) are not completely biodegradable, but they are made from plant-based raw materials, reducing dependence on fossil fuels. These plastics typically include Bio-PE and Bio-PET, made from biomass such as sugarcane or corn starch. They retain some of the properties of traditional plastics, making them particularly useful in fields requiring durability, such as food packaging.
Characteristics:
Not fully biodegradable but derived from plant-based sources like sugarcane or corn starch, reducing reliance on fossil fuels.
Common types:
Bio-PE (Bio-based Polyethylene)
Bio-PET (Bio-based Polyethylene Terephthalate)
5. Starch-Based Plastics
Starch-based plastics are made primarily from starch, often mixed with other bio-based polymers, and are widely used for lightweight packaging such as shopping bags and trash bags. Because starch is a renewable resource in nature, this plastic is considered a low environmental impact alternative. However, its physical properties are usually weaker and more prone to breakage, limiting its application scenarios.
Characteristics:
Primarily composed of starch, often blended with other bio-based or synthetic polymers.
Applications: Commonly used for lightweight packaging such as shopping bags and garbage bags.
6. Paper and Paper-Based Alternatives
While not plastic, many businesses are shifting to renewable paper bags or hybrid bags with waterproof coatings.
Advantage: Paper bags are heavier but offer superior recyclability and compostability.
7. Oxo-Degradable Plastics
Contain additives that accelerate decomposition into small particles through oxidation.
Controversy: These materials are debated due to potential microplastic pollution.
8. Ocean Plastics and Recycled Marine Debris
Made from plastics recovered from the ocean, helping to reduce marine waste.
Benefit: Contributes to ocean cleanup efforts.
9. Hybrid Bio-Plastics
Combine traditional plastics with bio-based materials to enhance performance, reduce costs, and improve environmental characteristics.